FORM, SURFACE MEASURING SYSTEMS
Thanks to our partnership with ACCRETECH – a manufacturer of the highest quality and most reliable technologies – we are able to supply instruments for inspections requiring the highest precision.
ACCRETECH products enable contact and non-contact measurement of SURFACE RUGOSITY, CONTOURS and SHAPE:
– Surface roughness: all parameters related to the required standards can be measured; the normally two-dimensional measurement can also be defined three-dimensionally with OPT-Scope optical products or by implementing laboratory roughness testers with an additional Y-axis for final scanning in three dimensions.
– Contour measurement: typical application measurements angles, bevels, radii, distances, threads with a resolution of less than 0.1 micrometre.
– Shape measurement: this includes the measurement of roundness, flatness, concentricity, coaxiality, runout, perpendicularity, cylindricity, parallelism and straightness.
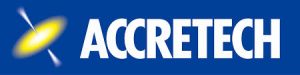
Accretech Catalogue

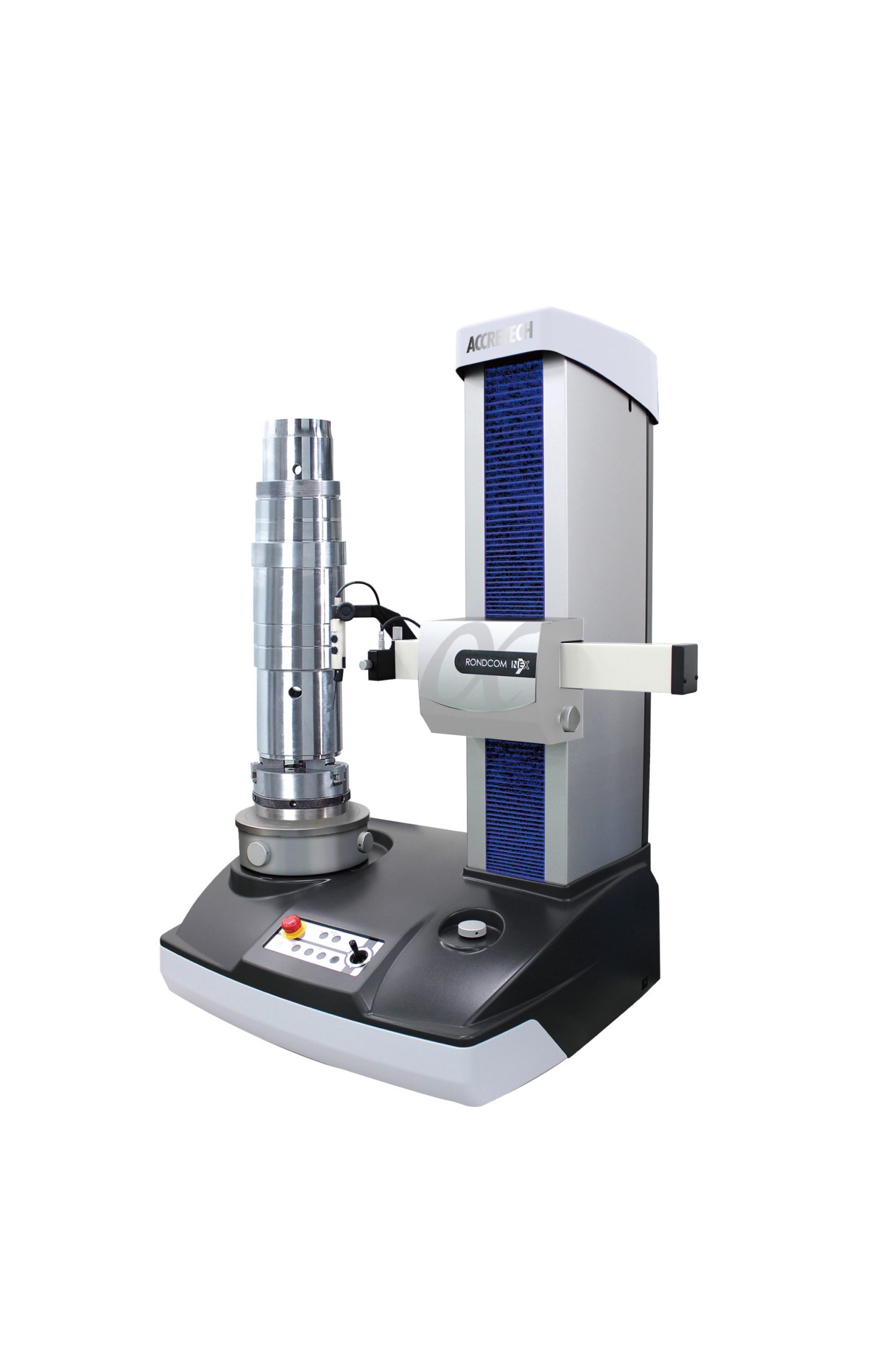
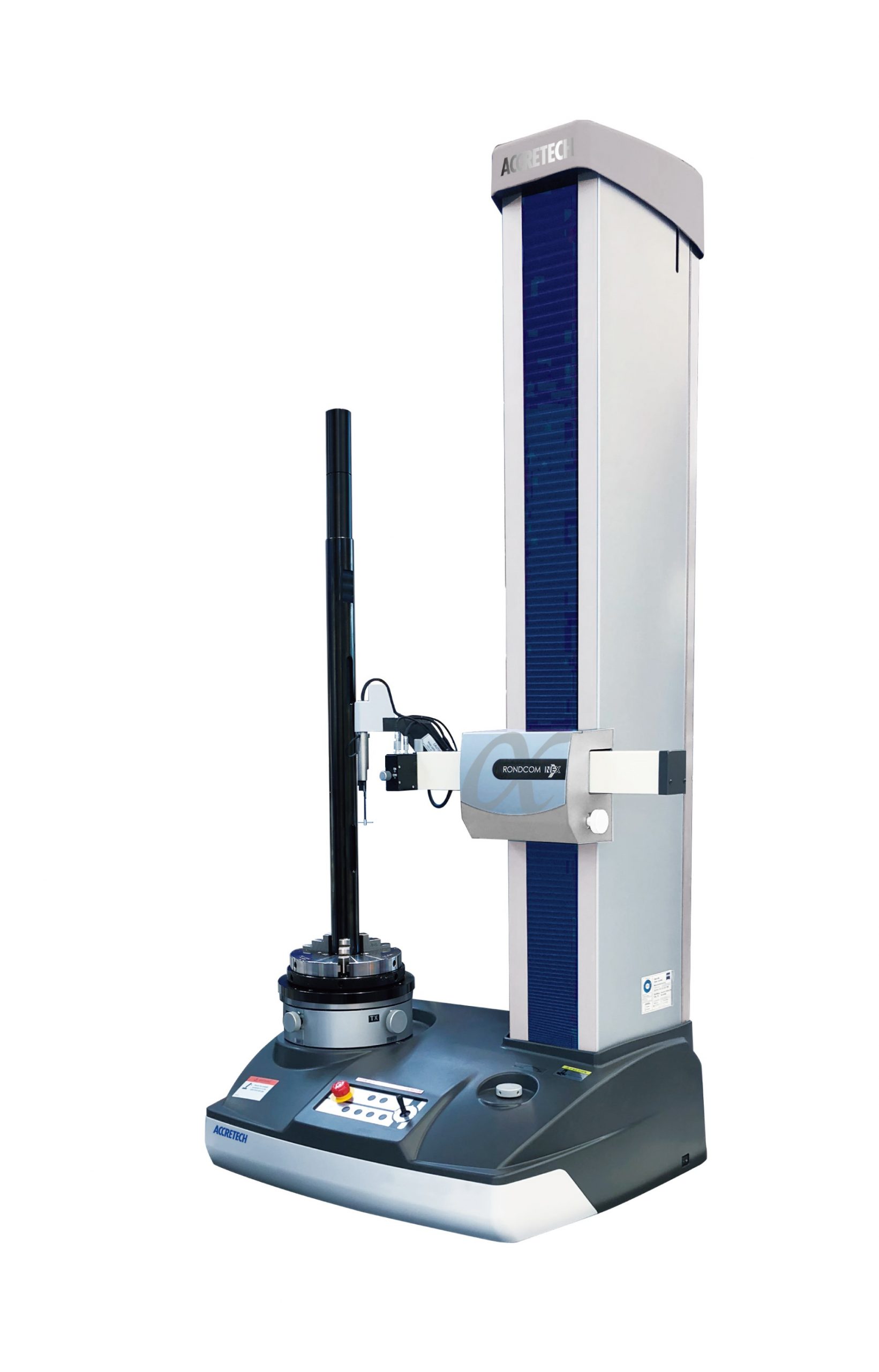
CNC-controlled profile measuring instruments
Experts from manufacturing and quality assurance are familiar with this dilemma: They have several dimensions to measure in a series of parts with a high throughput – and little time. The solution for this challenge is a fully automated, CNC-controlled profile measuring instrument with automatic workpiece alignment.
To ensure correct measuring results, the workpiece being measured must be carefully positioned under the measuring instrument. But even with multiple measurements, high parts throughput and time constraints, manually aligning the workpiece can be a source of problems. The advantages of automatic workpiece alignment are obvious: it saves time and reduces machine downtimes. Furthermore, it renders alignment devices unnecessary.
This is why ACCRETECH has developed a series of CNC-controlled profile measuring instruments that automatically perform workpiece alignment with the use of software. With the intuitive ACCTee PRO software, measurements can be programmed and the results evaluated and logged in graph form. Its unique feature is re-measuring at the press of a button.
The RONDCOM 60 profile measuring instrument is ideal for measuring cylindrical profiles on high-precision automotive parts. It is a roundness measuring instrument in the reference class for measuring with the lowest tolerance. Even the non-wearing, air-cushioned rotary table with 60 kg (or optional 100 kg) load capacity is ultra-precise with 20 nm. Especially on CNC-controlled machines that run round the clock, air bearings show off their advantage, as unlike friction bearings, they do not wear out. This makes the RONDCOM 60 extremely well suited for measuring small parts like injection nozzles, for example. Both the base and the column and R-axis are made from granite, which provides extra stability.
The RONDCOM 65 was specially developed for measuring cylindrical profiles on high-precision automotive parts, high-precision workpieces and calibration standards, as a profile measuring instrument with rotational accuracy of (0.01 +6H/10,000) µm. Its high level of precision is in part thanks to the non-wearing, air-cushioned rotary table for up to 60 kg (optional 100 kg) loads. The measuring range and probing force are both variably adjustable. The fast, automatic alignment enables high parts throughput.
With extremely high rotational accuracy, the CNC roundness measuring instrument RONDCOM Nex 200/300 offers fully automatic workpiece alignment. The
While the RONDCOM NEX 200 has automatic workpiece alignment and a manual turning/swivel probe head for measuring, the RONDCOM NEX 300 has a completely CNC-controlled probehead ensuring 100% automation at several different measurement positions/types. If desired, the RONDCOM NEX 200 can even be easily field upgraded to a fully CNC-capable profile measuring station later on.
The RONDCOM Nex Rs 200/300 is especially well suited for quality measurements on complex workpieces such as ball bearings. The advantage of this measuring instrument: It can be used to measure both profile and surfaces parameters reliably – in one clamping operation – at the same time according to ISO standards.
The RONDCOM NEX Rs is able to not only measure the position, profile and roughness in the R and Z direction, but also in the rotary axis. Measurement precision can be achieved in a way which was only possible with special roughness systems until now, due to its special air bearing concept with extremely low roughness.
Due to the modular design, the RONDCOM NEX 200 can even be converted to a fully CNC-capable profile measuring station later on.
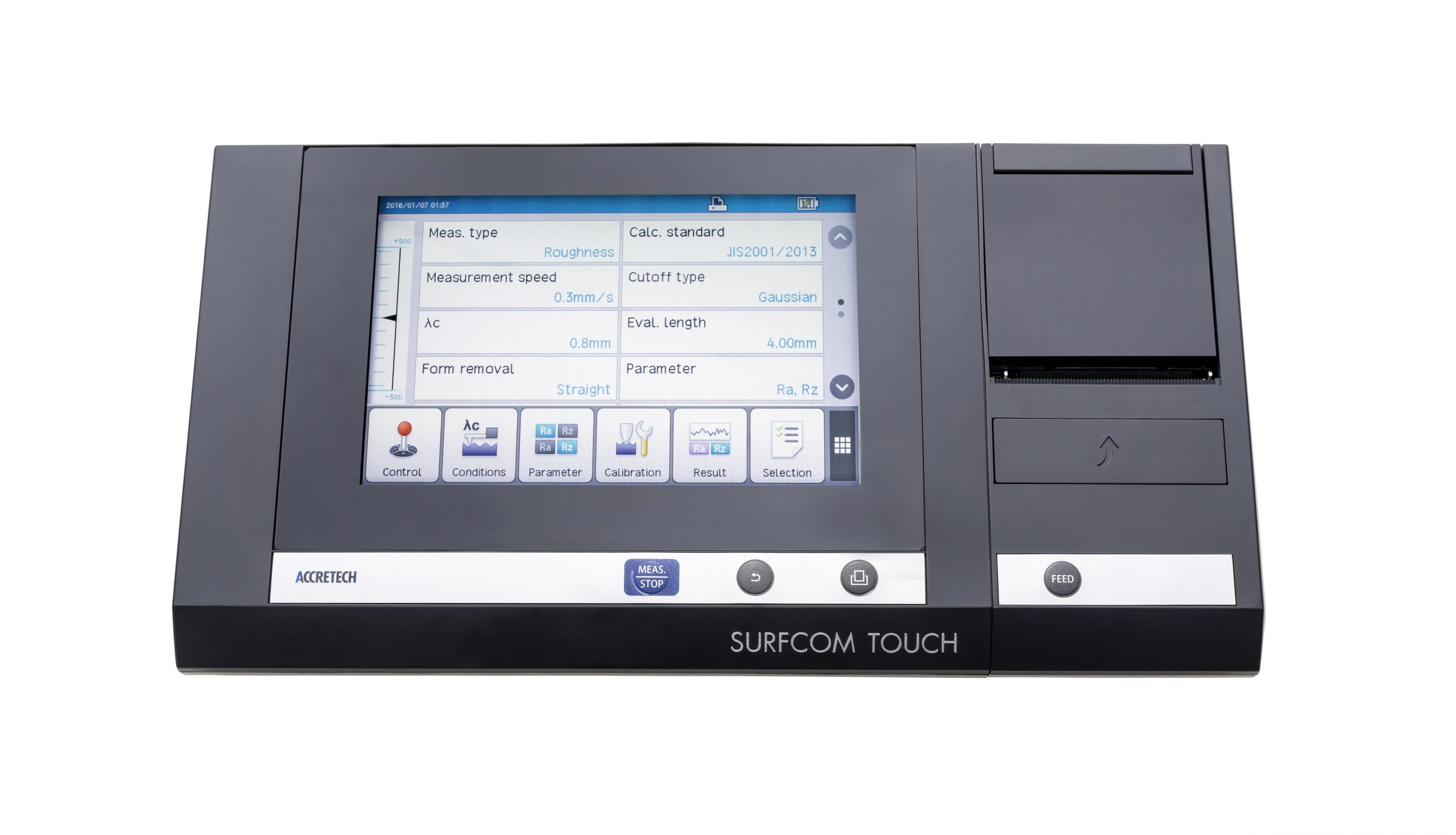
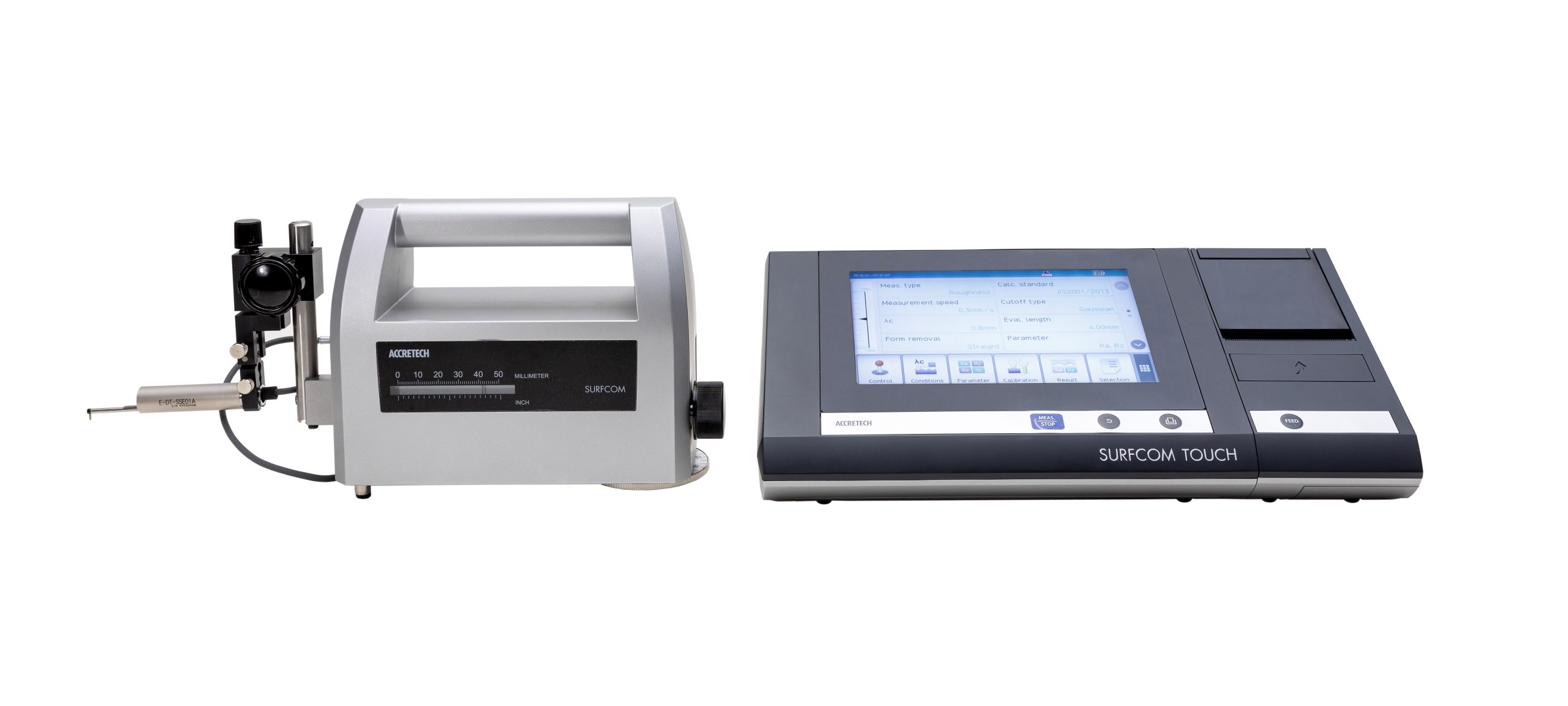
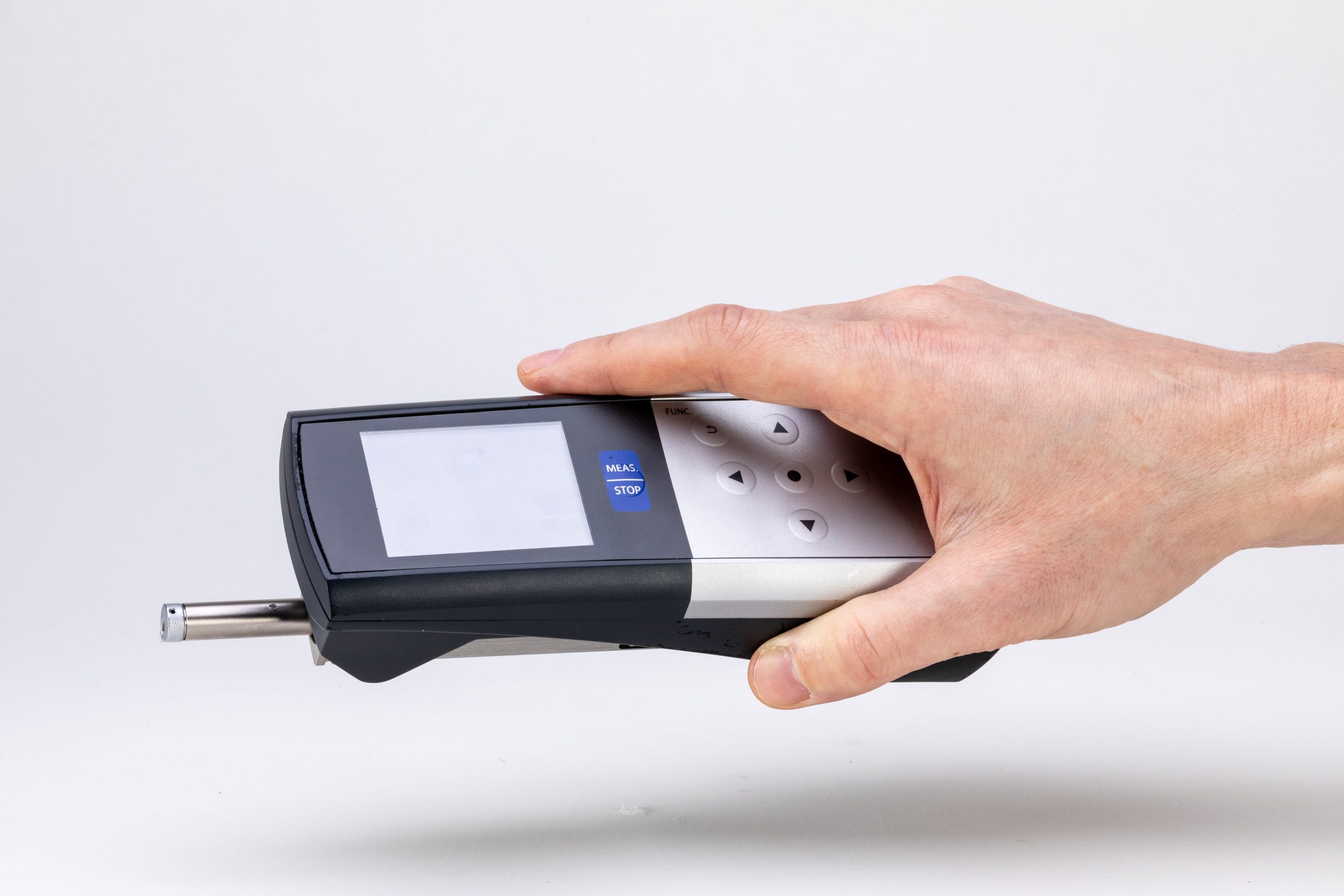
Roughness measuring instruments
Surface roughness is a measurement of the structure of a surface. It is calculated as a vertical deviation of the actual surface from its ideal shape and form, caused by machining or by chemical or physical processing in production. If these deviations are high, the surface is rough. If the value is low, the surface is smooth. Surfaces vary from part to part which is why the selection of the most fitting surface roughness measurement solution is essential.
Measure surface roughness according to all important standards
Many parameters can be used to describe the texture of surfaces and profiles. The peak/valley parameters most often used, such as Ra, Rz or curve parameters such as RMR are described in the norms DIN EN ISO 4287/4288 and DIN EN ISO 13565-1/2 for physical metrology. DIN EN ISO 3274 describes the parameters and operators regarding their definition for optical 3D surface measurement. If the sampling length for example is not given, the ISO norms help to define the calculations.
With the ACCRETECH gauging systems for roughness, deviations from the target surface texture can be detected with nanometre-precise certainty – in both manufacturing and in the measuring room. Tactile measurement and the stylus tip have hereby contact to the workpiece and is able to measure in nanometre range.
ACCRETECH provides roughness measuring instruments for a wide variety of requirements and in various designs: The convenient mobile gauge in the HANDYSURF+ series form the entry level, followed by portable models 35, 40, 45 and 50 from the SURFCOM TOUCH series for higher requirements. In addition, there are three stationary roughness measuring systems (the SURFCOM TOUCH 550, the SURFCOM C5 and the SURFCOM NEX 001) for use in manufacturing environments or in the measuring room.
Due to the elimination of the drive shaft and the drive gears in the feed, the inspection gauges from ACCRETECH work at a low vibration with a resolution of up to 0.31 nm. Another major advantage of the linear technology, which requires little servicing and maintenance, is the durability of the system and therefore the extraordinary cost efficiency.
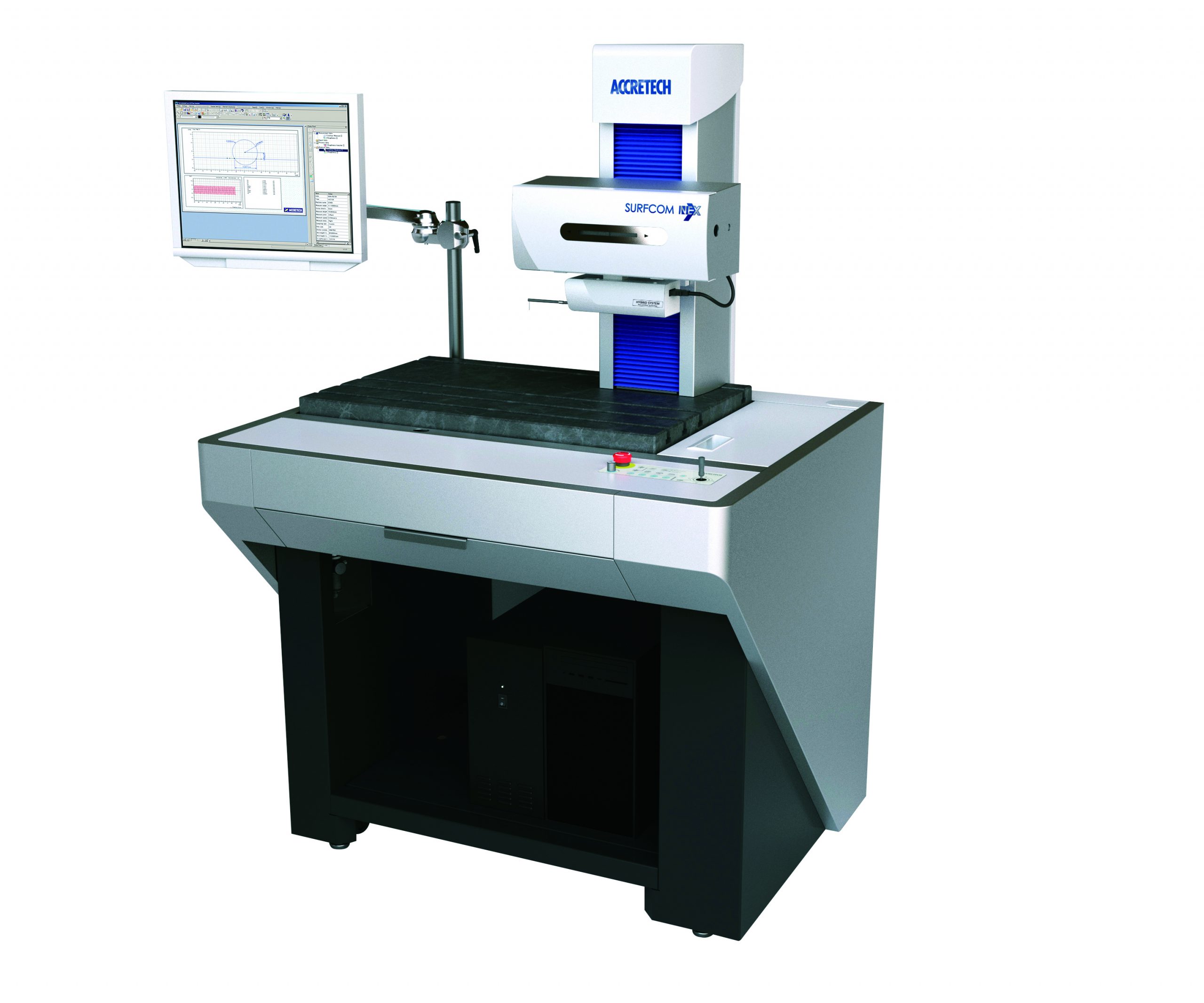
Contour measuring instruments
Angles, radii, distances and coordinates of work pieces can be determined with the highly precise ACCRETECH contour measuring systems.
Due to the elimination of the ball screw and the nut, the inspection instruments work at a low vibration with a resolution of up to 0.31 nm. Another major advantage of linear technology, is it requires little maintenance and will maintain the measurement accuracy over the life of the gauge much better than tradition ball screw approach due to the reduction in mechanical wear. This gives our customers enormous cost savings over the life of the system.
The SURFCOM NEX 030 and the SURFCOM NEX 040 contour measuring systems are available for two-dimensional, tactile contour measurement. These are both flexible CNC measuring stations for various measurements. SURFCOM NEX 030 with a measuring accuracy of ±(1.5+|2H|/100) µm, standard version is suitable for measuring all contour geometry and surface of standard work pieces. SURFCOM NEX 040 with a high measuring accuracy of ±(0.8+|2H|/100) µm, suitable for measuring highly precise contour geometry such as ball screws or ball bearings.
ACCRETECH keeps a wide range of stylus for contour measuring gauges on hand so that even hard to reach geometries can be measured. Stylus can be swapped out quickly thanks to kinematic magnetic holders with high positioning accuracy. Profile, roughness or contour measurements are easy to conduct, and the process is efficient.
The software for operating the profile gauge tools is deliberately kept simple and self-explanatory. Measurements of roughness or surface for example are fully automated. Even calibration and adjustment are easy for the user to do, which saves times.